Traditional thermal transfer technology
Traditional thermal transfer technology
Thermal transfer is a printing process that has been popular in China for less than 20 years. It was introduced to my country from abroad in the 1990s. After continuous efforts, exploration and research by peers in the industry, it has become a mature and rapidly updated printing process. Because this process has great advantages in controlling production costs and improving product appearance, it is highly respected and continuously developed in the printing industry.
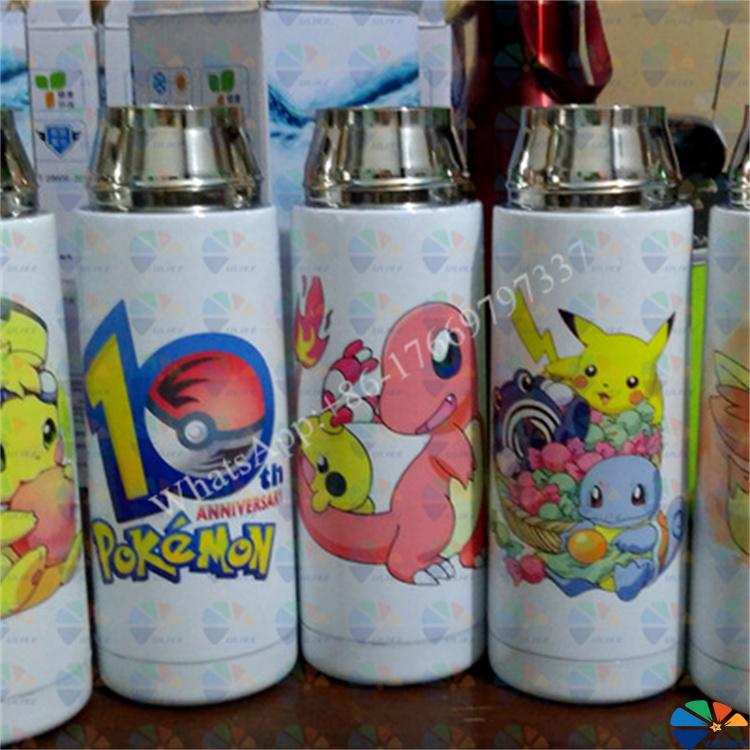
1. Introduction to thermal transfer technology
The thermal transfer printing process is divided into two parts: thermal transfer film printing and thermal transfer processing.
1. Thermal transfer film printing:
Most of them use precise gravure printing technology, and the resolution of the printing dots can reach 300 dpi. The pattern is pre-printed on the surface of the transfer film. The printed thermal transfer film pattern is rich in layers, bright and full in color, with small color difference and better reproducibility of pattern effects, which can meet the requirements of pattern designers.
2. Thermal transfer processing:
Through a one-time processing of the thermal transfer machine (according to the working principle of the thermal transfer machine, the thermal transfer film is heated and pressurized simultaneously), the exquisite pattern on the transfer film is transferred to the surface of the substrate (including flat and curved surfaces). After forming, the pattern is integrated with the product surface, and the transfer film falls off naturally, and the process is completed.
Because the traditional thermal transfer printing process is green and environmentally friendly, meets international standards, the printing pattern effect is realistic, the color is bright and saturated, the product is exquisite and beautiful after forming, the pattern has strong adhesion, long-lasting wear resistance, not easy to fade, less production loss, low cost and other advantages, it is widely used in the surface decoration and packaging decoration of cosmetics, toys, electrical appliances, household building materials, stationery, gifts, accessories, daily necessities and other products with large batches and high requirements. Applicable materials include plastic products such as ABS, AS, PS, PVC, PP, PE and metal, glass, and wood products.
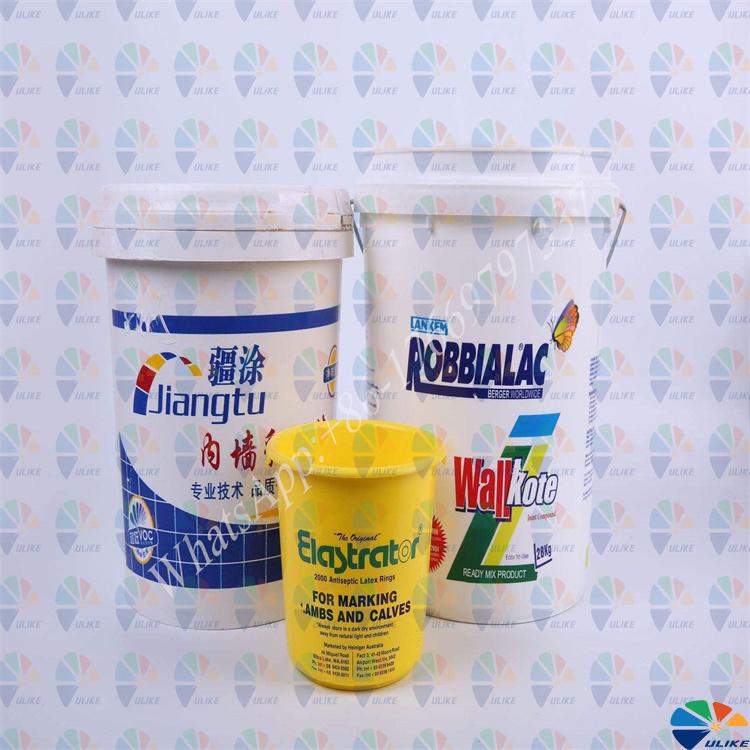
2. Technical advantages of traditional thermal transfer technology
The rise of new transfer technologies such as in-mold labeling, in-mold transfer, vacuum transfer, thermal sublimation, and water transfer has a great impact on traditional thermal transfer technology, but the use of traditional thermal transfer technology is still prosperous. It is widely used in cosmetics, toys, electrical appliances, household building materials, stationery, gifts, accessories, daily necessities, etc., especially in cylindrical, conical, curved and other shaped workpieces, such as lipstick shells, pen refills, finger snowboards, conical lampshades and other product fields. Traditional thermal transfer has shown its irreplaceable side. Even for flat objects, there are many processes that can be printed, but traditional thermal transfer can still show advantages in many aspects.
The first point is high efficiency
Take the Rubik's Cube as an example. The Rubik's Cube has six planes. If other types of printing technologies are used, there must be a process of waiting for drying or natural drying. In this process, some places are bound to be needed to store these process products. Thermal transfer is different. It can be printed continuously without drying. After printing, it can be packaged. The production site is greatly reduced and the production efficiency is greatly improved.
The second point is rich colors. Taking the Rubik's Cube as an example, the traditional Rubik's Cube pattern has only a single color block on each plane, and the color and pattern are relatively monotonous. Traditional thermal transfer is different. Since the pattern is first printed on the PET thermal transfer base film, the color of the pattern can be reproduced almost without restriction. Various patterns of flowers, trees, people, landscapes, etc. can be transferred to the Rubik's Cube, which greatly enhances the appearance of the Rubik's Cube and the added value of the product.
The third point is environmental protection. Whether it is the base film or the selected printing ink, release layer, adhesive and other materials, the traditional thermal transfer film can pass the environmental protection test of domestic and foreign testing agencies (BV, SGS, etc.). In the production process, thermal transfer is also extremely low in noise pollution, and almost zero in sewage and waste gas pollution. This is one of the reasons why the traditional thermal transfer process is popular and different from other printing types.
The fourth point is the rich combination
The fourth point is also the most important point, that is, the combination of traditional thermal transfer processes is relatively rich. In addition to the simpler ordinary thermal transfer process, the product process combination can also be refined to form a combination of thermal transfer processes such as high cutting edge, UV-friendly, steaming resistance, anti-bending, ethanol resistance, high hardness, high wear resistance, matte, partial aluminum plating, partial laser, transparent laser, metal texture, etc. It is suitable for high-end surface decoration of plastic, wood, leather, and metal workpieces.
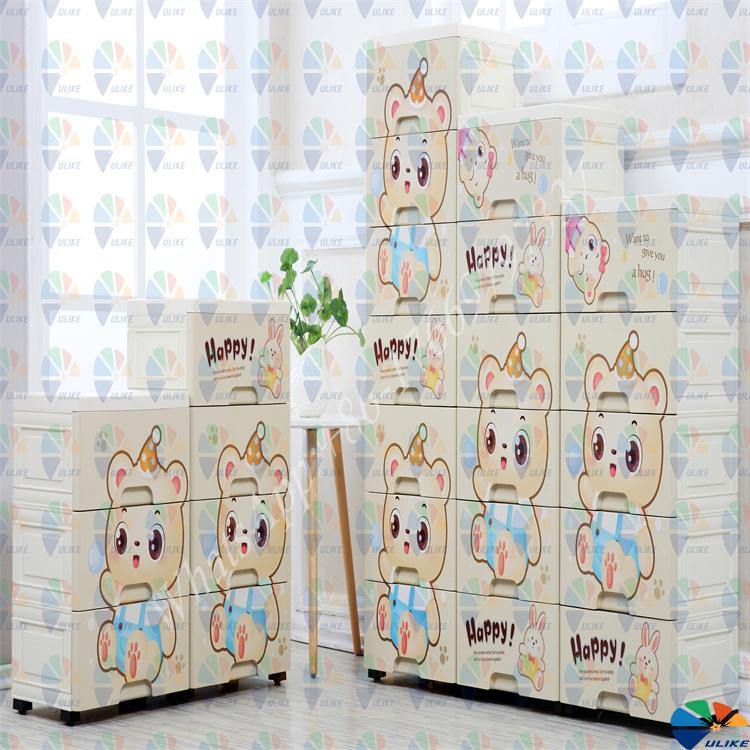
In addition, with the continuous optimization of traditional thermal transfer process technology, the process technology of traditional thermal transfer machines has also been rapidly developed. Many thermal transfer workpieces with higher transfer difficulty can be transferred, such as conical surfaces, curved surfaces, arc triangles, S-shaped surfaces with smaller arcs, and other more difficult workpiece surfaces. Transfer can be achieved. As a result, swing-arm thermal transfer machines, taper thermal transfer machines, contoured rolling thermal transfer machines, curved thermal transfer machines, and various tooling components and fixtures with different functions have been developed, which have derived many hot stamping functions to meet the transfer needs of workpieces of various shapes.