In-Mold Labeling (IML) in Popcorn Cups: Applications and Benefits
In-Mold Labeling (IML) has become an essential technology in the food packaging industry, particularly for products requiring high-impact visual appeal and durability. In the context of popcorn cups, IML offers a premium solution for branding, product differentiation, and compliance with food safety standards. This article delves into the specific applications and benefits of in-mold labeling in the production of popcorn cups, focusing on how it enhances both functionality and consumer appeal.
In-mold labeling is a process where a pre-printed label is placed into the mold used to shape a plastic product. During the molding process, the label fuses with the plastic, creating a single, seamless product. This integration ensures that the label becomes a permanent part of the popcorn cup, providing superior resistance to wear, moisture, and other environmental factors that can degrade traditional labels.
-
Branding and Aesthetics
-
Popcorn cups are often used in settings like cinemas, sports arenas, and events where branding and visual impact are crucial. In-mold labeling allows for the application of high-definition, multi-color graphics that cover the entire surface of the cup. This capability is particularly valuable for brands looking to create a memorable and visually appealing experience for consumers. The ability to include intricate designs, logos, and even photographic images enhances brand visibility and consumer recognition.
-
Durability in High-Usage Environments
-
Popcorn cups are typically exposed to frequent handling, heat from the popcorn, and potential moisture from butter or other toppings. IML provides a durable labeling solution that resists scratching, peeling, and fading, ensuring that the branding remains intact throughout the use of the product. This durability is crucial in maintaining the cup's aesthetic appeal, especially in high-traffic environments.
-
Compliance with Food Safety Standards
-
Since in-mold labels are integrated into the plastic during the molding process, there is no need for adhesives or additional materials that could potentially compromise food safety. This makes IML an ideal choice for popcorn cups, as it ensures that the labeling is non-toxic, free from contaminants, and safe for direct contact with food. Additionally, the seamless nature of IML prevents the label from becoming a potential harbor for bacteria, further enhancing the product's safety profile.
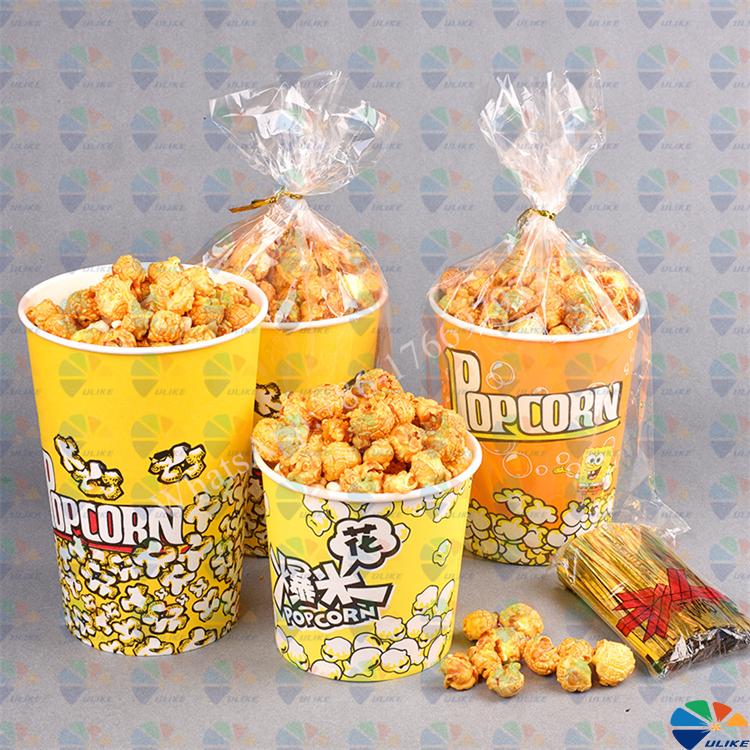
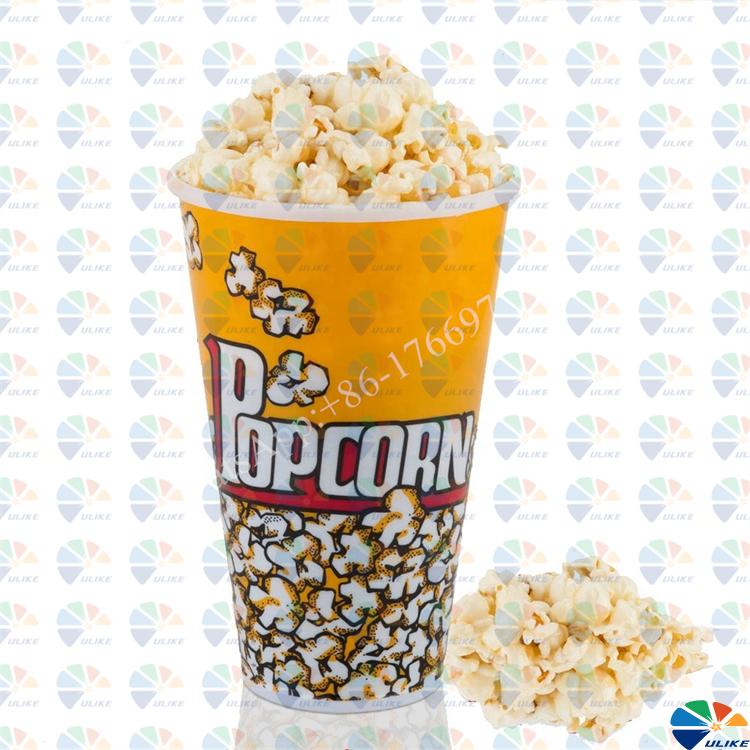